Let there be light (and a bit of control)
Back in 1879 Thomas Edison finally perfected a commercially viable design for the electric light bulb, heralding the start of a global transformation that would see instantaneous light eventually become the expected norm for most of us on planet Earth. Today we take it for granted that if we want light we simply flick a switch and hey presto, problem solved…….hold that thought.
Nobody, least of all me, can accuse Edison’s breakthrough of being anything less than a game changer, but a light source without any control could be considered almost as much a problem as it is a solution. It’s all well and good bestowing the gift of instant light on a grateful world, but what about the times when some good old fashioned darkness is desirable; when trying to sleep for example?
In 1886 Karl Benz designed the first petrol powered car, but he had the foresight to include a set of brakes because he realised that at some point the driver might just need to, well, stop. Whitcomb Judson’s ‘clasp locker’ invention (zip to you and me) in 1893 was bi-directional because he knew that if somebody put on an item of clothing and zipped it up, there’d be more than a strong possibility that they’d want to be able to take it off again in the not too distant future. Fortunately, a young engineer, John Henry Holmes from Newcastle-on-Tyne, would soon provide the perfect addition to Edison’s light bulb by inventing the ‘quick-break’ switch, which he duly did in 1884. His ground breaking design ensured the contacts opened or closed very quickly, regardless of the force exerted by the operator on the actuator, which significantly reduced the amount of arcing inherent in previous incarnations, subsequently prolonging the working life of the switch. Thus, the humble light switch was born and ever since we’ve been able to turn the bedroom light off.
The same, but different
Aesthetically, the light switch has clearly evolved since the advent of the quick break switch, but the principles behind its operation have remained fundamentally the same. Proof, perhaps, that John Henry Holmes was an engineer of some repute, despite being less of a household name than Thomas Edison, Joseph Swan et al.
If the mechanics of the light switch haven’t changed much per se, the methods and materials employed when wiring to it certainly have. No longer will VIR and waxed cotton covered conductors protected by nothing more than a bit of fuse wire in porcelain carrier suffice as would have been the case when the light switch was in its infancy, oh no. If you want to comply with current wiring regs, which I’m guessing everyone reading this does, then there’s a good chance that today’s switch drop will require not only earthed mechanical protection, but RCD protection as well, depending on the particular characteristics of the installation. Section 522.6 of BS 7671 details these requirements in full and compliance will almost certainly result in the need for additional materials, labour and, inevitably, the costs associated with purchasing and installing them.
Having said all that, if you’d rather avoid installing earthed metallic and/or RCD protection to literally every switch drop, yet still comply with BS 7671, the afore mentioned Section 522.6 obligingly provides a means of doing so in the form of regulation 522.6.204, indent (v), which reads:
“For the purposes of Regulation 522.6.201 (ii), Regulation 522.6.202 (ii) and Regulation 522.6.203 (ii), a cable shall:
- (i) ……………………
- (ii) ……………………
- (iii) ……………………
- (iv) ……………………
- (v) form part of a SELV or PELV circuit meeting the requirement of Regulation 414.4”
For the sake of clarity, indents (i) to (iv) inclusive detail the need for the cable in question to be protected by an earthed metallic covering in various guises, hence the reason for not detailing them on this occasion.
Popular misconceptions
You may be of the opinion that installing a PELV control system is a costly exercise, not to mention complicated, and that sticking with the more familiar 230 volt option is probably best, but in reality nothing could be further from the truth. The flex7 System incorporates PELV control as standard meaning that any wiring to a connected control device, be it a switch or a sensor, requires neither mechanical nor RCD protection, regardless of cable location. Furthermore, because the link from controller to device is made via factory prepared leads complete with RJ connectivity there’s no on-site cutting, stripping and terminating required; everything simply plugs together. In short, opting to go down the PELV route can make for a quick, easy, error free install with the added bonus of reducing materials and labour.
'Opting to go down the PELV route can make for a quick, easy, error free install with the added bonus of reducing materials and labour.'
Plug-in the gap
Since their inception in 2003, all flex7 sensor heads have incorporated RJ connectivity and operated at PELV; a feature which has been well received by the market in general. However when it comes to a switch lead, although one end plugs into the controller in exactly the same way as a sensor lead, the third party switch at the other end is invariably a standard catalogue product from one of the mainstream accessory manufacturers and as such has to be connected using the time honoured method of screwed terminals. Clearly, it still operates at PELV (5 volt in this instance) courtesy of the controller upstream, but is no quicker to physically connect up than any common or garden switch.
In July 2017 we launched our own scene set plate to complement the flex7 System and because, as you’ve probably realised by now, we think plug-in control is a better option than hard-wired, we built RJ connectivity into it as standard. Subsequent feedback from installers has been extremely positive, however one comment has rung out loud and clear: “You should do switches like this!” We’ve listened and have developed a range of momentary switches that, as is the flex7 way, operate at PELV, plug-in at the control pack and, uniquely, plug-in at the switch as well and in doing so have probably brought about one of the biggest changes the light switch has seen in more than a hundred years.
Why make the switch?
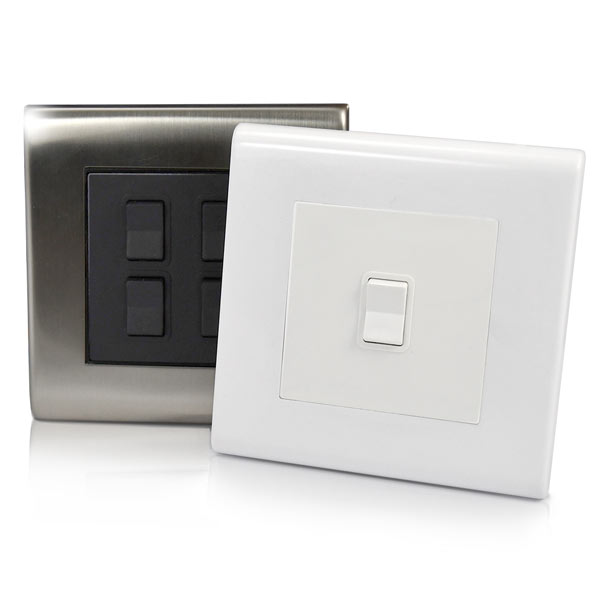
In keeping with our scene set plate, flex7 momentary switches come as standard in a black or white finish and are designed to clip directly into any manufacturer’s 50 x 50 Euromod decorative fascia, ensuring seamless integration with the specified accessories – should keep the architects happy. Whether using a 1,2,3 or 4 gang variant, a standard single back box with 60.3mm centres is all that’s required, so no need to choose between single or double at first fix stage; one size really does fit all.
Because the lead is factory prepared with the RJ plug, connecting the switch quite literally takes a second, as opposed to the minute it probably takes on average to terminate a conventional 230 volt, 1 gang 1 way; stripping the sheath, baring the conductors, sleeving the earth, connecting via screwed terminals. Add to the equation that there’s already been a considerable saving with respect to labour as a result of opting for a PELV system in first place and it’s fair to say that the opportunity to reduce switch installation time to a minimum has never been so attainable.
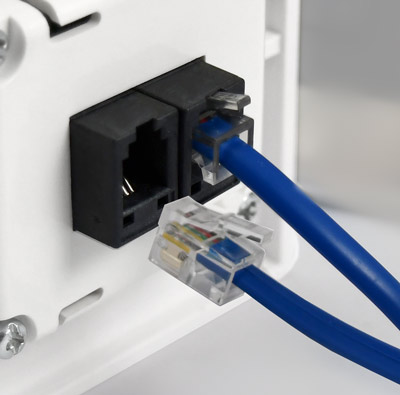
Simple Connection via RJ11
The ability to mix and match module colour with a myriad of decorative fascia’s from the majority of accessory manufacturer’s not only means that the intended ’look’ need not be compromised, but, in the spirit of Part M2, Section 4 of The Building Regulations, also makes it possible to achieve a colour contrast between switch, fascia and wall finish to aid partially sighted users if required. Furthermore, because the hard work of opening and closing the contacts is done at the controller, there’s no need for strong springs and large contacts at the switch (apologies to John Henry Holmes at this point) so the user doesn’t need to exert excessive force to turn the lights on/off; a light (no pun intended) press is all that’s required.
Not the end yet
Despite a flurry of recent articles in the trade press predicting its imminent demise due to the rise of smart lighting and all things IoT, that familiar old light switch that we instinctively fumble for as we enter or leave the room will remain a familiar fixture in our everyday lives for a good while yet. In fact, I’d be as bold to say that I can guarantee tens of thousands will be installed in building projects up and down the UK in the next 12 months alone.
It’s often said that familiarity breeds contempt and although contempt in itself is a bit strong for the way we might feel about light switches, it’s probably fair to say we don’t pay them too much attention; they’re not new or high tech or sexy, they’re just………there. For the people using them, Mr & Mrs Public, that view point will undoubtedly remain the same, but given that we’ve established light switches are going to be a common feature in virtually every building for the foreseeable future, engineers still have to deal with the practicalities of installing them. That being the case, employing the most efficient methods of doing so would seem to be a good idea for specifiers and electrical contractors alike, and the new flex7 plug-in switches would appear to tick most of the necessary boxes on that front. Were he still around, we’re sure John Henry Holmes would approve.
More On The Author
Paul Bellamy been involved in the electrical industry all his working life, initially in contracting, before moving into manufacturing. With his wide range of industry knowledge amassed over 40 years, he is now managing Director of flex7. Paul has been with the company since its early years and is the brains behind some of flex7’s most innovative products.
More On The Plug-in Switches
flex7 have developed a unique range of plug-in switches that operate at Protected Extra Low Voltage (PELV) and offer the installer dramatic time savings. Find out more on our switches on the switches product page.
Leave A Comment